Leading a revolution in manufacturing in London, BLOQS is the UK’s first open-access factory, offering pay-as-you go accessibility to makers.
The BLOQS site in London’s Lea Valley houses £1.3 million worth of light industrial equipment, including comprehensive wood processing & metal fabrication, engineering mills & lathes, CNC machining, 3D printing, and sewing machines catering for a range of professional makers across woodworking, metalworking, fashion, engineering, product design, event production, construction and architecture.
With backing from the Mayor of London and sitting on an advisory board for MAKE UK, BLOQS is disrupting manufacture with a “WeWork” model for the maker economy of today. The partnership between the founders of BLOQS and Enfield Council has created a blueprint for city regeneration of neglected industrial sites, sustainably creating jobs, and fostering creativity with a modern community-centred ethos.
With pay-as-you-go access, entrepreneurs can utilise this state-of-the-art equipment as and when they need it, eliminating the burden of fixed and high overhead costs, reflecting the increasing trend of the sustainable ‘sharing economy’, which is expected to be worth £140 billion by 2025. It also reflects the growing public desire for bespoke items, or products manufactured with a lower carbon footprint.
“BLOQS provides the missing link for solopreneurs and SMEs seeking to bridge the gap between start-up and producing at scale,” says Al Parra, Co-Founder at BLOQS. “Our space empowers, fostering growth that remains rooted in the community.”
Sustainability has been designed into the BLOQS infrastructure itself. All energy from wood waste is recovered by a biomass boiler and used for space heating, central heating, and the building’s various hot water needs. And recently installed state-of-the-art solar panels to the roof provide 35% of the site’s electricity.
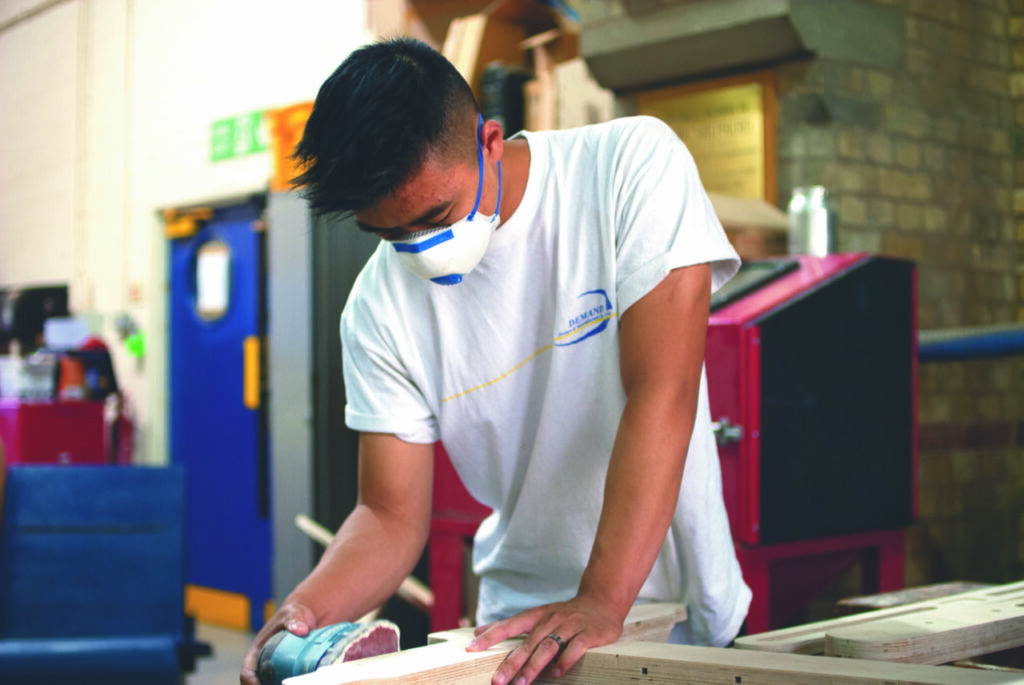
“BLOQS is a social enterprise whose purpose is the creation of social and economic capital for the communities it serves, whilst being frugal with the planet’s increasingly scares resources. We take environmental stewardship seriously, as we look to regenerate urban creative economies by seeding maker hubs where creatives can learn and thrive together” adds Parra.
Currently, the scheme has created 380 full-time equivalent jobs and £15m a year is generated in the local economy by BLOQS members. In the furniture making space, BLOQS revealed around 500 members are involved that make free standing to fitted, hard wood to soft wood to composites, commercial and domestic, community and designer products.
Parra continues: “It’s a dream ecological factory for furniture makers – packed with top end equipment, people to teach you how to use it, the place is clean and bright, loads of natural light, surrounded by peers, lots of new technology alongside knowledgeable experience, a supply of materials, helpful staff, handy technicians, a raft of services, and a café bar to eat in and meet clients. All this and more, and with no fixed over heads.
“As well as the obvious woodworking department our furniture makers value our bookable spray booths and drying room, the 5-Axis CNC, our tube and pipe bending machines in the metal work department, engineering lathes, sewing machines, laser cutters, 3D printers, design software classes and a copious supply of Gorilla Glue.”
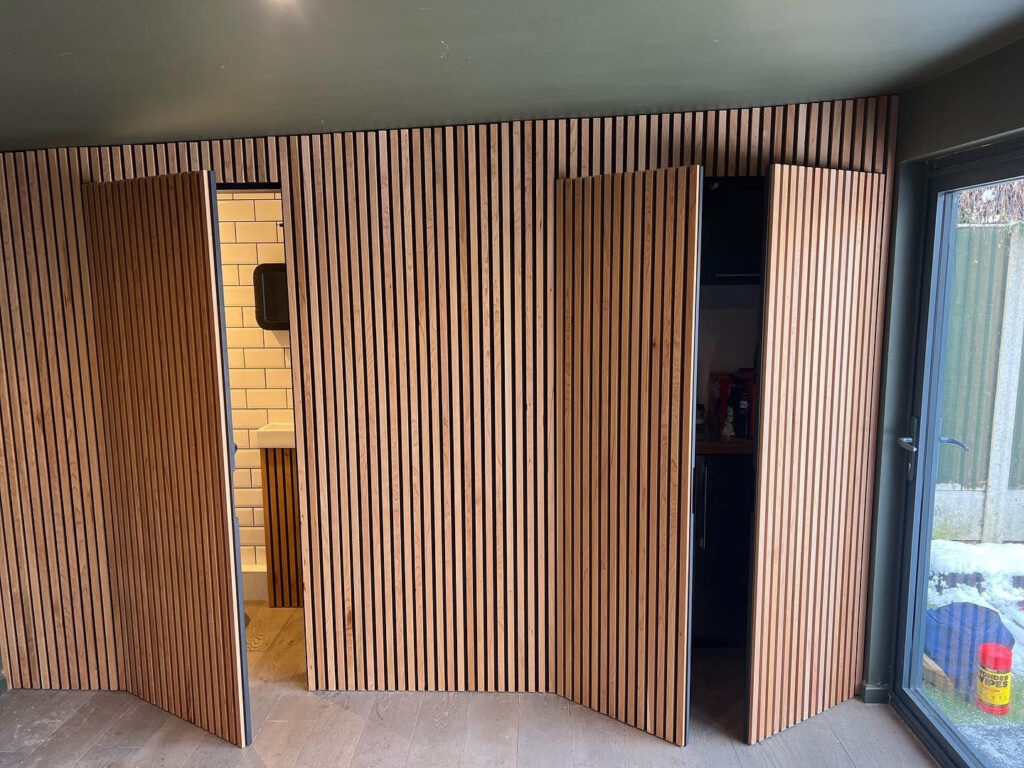
Two such members that are benefiting greatly from the enterprise include DWC Carpentry and DEMAND. DWC Carpentry is made up of David and Billy Chamberlain, a father and son team and the fourth and fifth generations from a lineage of carpenters stretching back over a century. Based In stoke Newington, they work in a variety of carpentry and joinery areas ranging from full bespoke wardrobes, bookcases and entertainment media units to general carpentry projects. “Joining BLOQS eight years ago has allowed us to broaden our offering without the additional expense of running our own workshop and benefit from the community of other friendly co-workers,” Billy Chamberlain from DWC Carpentry says.
As for DEMAND, they create unique, effective and enabling assistive equipment. Its mission is to help people live life their way; to overcome barriers to independence and to enable them to access life enriching opportunities for study, travel, work, sport and leisure. Their Freasel accessible artists easel is made in small batches using BLOQS’ 3 axis CNC router and is helping disabled artists paint and create comfortably from a wheelchair or bed without having to reach out to the canvas. DEMAND’s Lynette Smith said: “Being at BLOQS has massively improved our production flow. The bulk of DEMAND’s production currently relies on intricate routered plywood shapes, those that make up our Sensory Shell rocking chair for example. We’d used a CNC router for several years to manufacture our products but it’s nowhere near the reliability of BLOQS’ Holz-her, which is a real professional beast.”
For makers keen to get involved, the process is simple by just heading to the BLOQS website and clicking ‘join’ to get the process started. Parra said that BLOQS London is just the beginning of the journey, adding: “If we’re not in your area yet and you’re keen that we should be, get in touch. We’re opening branches where we’re needed and aim to help makers wherever they are with innovative support and learning resources. Our model ecologically democratises resources so that people can unlock their creative potential, invent, innovate, design, and grow prosperity.”
www.bloqslondon.com / www.dwccarpentry.co.uk / www.demand.org.uk